プレス加工について
㈲スリーサプライ川口には75tプレス機が2台、50tプレス機が1台、そして25tの小さなプレス機が1台あります。
計4台が毎日フル稼働しています。
一番大きな75tプレスは、横幅が1メートルのワークにも対応できます。
一昔前のトムソン型(ビク型)を使ったプレスは、精度を要求されることはほとんど無く、1日1,500パンチ~2,000パンチのプレス作業が当たり前の、数で勝負の部署でした。
しかし昨今、トムソン型の精度が上がり金型プレスとの差がなくなってきました。
また、エッチングで作成するピナクル型の刃高も1.2mmから2mmとなり、厚物のプレスが可能となりました。
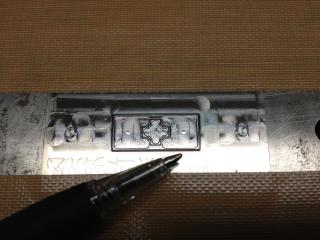
トムソン型とピナクル型の使い分けの目安として、±0.15mm以上の仕上がり公差であればトムソン型。
±0.1mmの場合はピナクル型を使用します。
また、ビク刃のつなぎ目のあとが製品外周に残ってはいけない場合はピナクル型を使用します。
トムソン型(ビク型)の優位な点は、その価格の安さにあります。
例えばトランプの抜き型を作成するとして、金型の場合は1面型でも価格は20万円ほどになるでしょう。
対して1面トムソン型の場合は10,000円ほど。5面型にした場合でも25,000円程度で作成できてしまいます。(正式な見積もり価格ではありません)
さらに多面型にすることで製品1pcsあたりのプレス工賃も安くなります。これは当然製品価格に反映されます。
そんな理由から、公差±0.1mmで設計した図面を±0.2mmに変更してトムソン型で加工するといった事例が増えています。
抜き位置の精度
製品の仕上がり寸法の精度の要求の他にプレス位置の寸法精度を要求される製品が多くなりました。
LED窓から外形端面までの寸法。7セグ窓から外形端面までの寸法公差が0.2mm以下の製品は珍しくありません。
このような印刷意匠に対する抜き位置の精度は、ガイド穴をあける精度に大きく依存します。
かなり以前は、"蹴飛ばし"と呼ばれる足蹴り式の穴あけ機でガイド穴を開けていました。
これは人の目で印刷されたガイド穴めがけて穴をあけていたので、穴あけ精度は±0.3mmにおさまれば上出来といった感じでした。
そのため、抜き位置の寸法精度を保つことは困難でした。
その後、スコープのついた穴あけ機が登場し、ガイド穴の精度が飛躍的に向上します。
そして極めつけが下写真の自動穴あけ機です。
内部のアセンブラのプログラム上では、1,000分の1mmまで計算されていると思われます。
ワークは厚みがあり、裏面がシリコンで滑る製品も多いです。
エンボス等でバキュームテーブルの吸着の悪い製品もあります。
そのあたりを加味すると現実的な自動ステ穴機の精度は±0.1未満といったところでしょうか。
ガイド穴の精度アップに助けられて、プレス位置の寸法精度も安定するようになってきました。
しかし実作業で定位置にセッティングするのはプレスオペレーターです。
そして試抜きした製品の抜き位置のチェックを行うのもプレスオペレーターです。
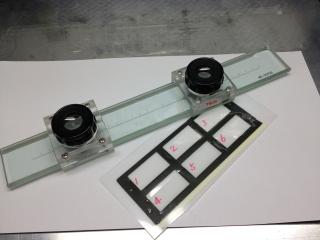
スリーサプライのプレス加工部門ではガラススケールで製品寸法と抜き位置寸法の確認をします。
0.1mm単位での寸法確認は難易度を要します。
また当然ですが製品図面を正しく読めるスキルも必要とします。
抜き位置の調整で0.1mm手前に…、0.15mm左に…、と微調整できるようになるまでには、はやい人でも半年ほどかかります。
印刷機のように微調整機能の無いプレス機でのセッティング作業(抜き位置の微調整作業)は非常に難易度が高いのですが、それを簡単にする工夫があります。
スリーサプライで考案した独自の方法です。
セッティング時間の大幅な短縮と、0.1mmの横移動などを1回の調整で済ませる方法があるのです。
詳しくは別ページでご紹介します。